How does an expensive grinder differ from a cheap one?
We independently test the products and technologies that we recommend.

Grinder class
The most obvious difference between expensive and cheap grinders is the fact that they belong to different classes of tools and are initially designed for different operating conditions. On a conventional scale on which you can place all angle grinders found on sale, there are two extreme points: “professional” tools and “home use” models.
- Professional angle grinders are tools designed for long-term non-stop work with heavy loads and in difficult conditions. They are indispensable in metalworking shops for tasks like stripping and grinding sheet metal and profiles in constructing metal structures. Similarly, they are vital on construction sites for cutting pipes, fittings, and various building materials. These grinders are designed to operate almost continuously throughout shifts, only stopping briefly to change cutting discs or grinding wheels.
- Home grinders are suitable for less frequent use, ideal for garage or home workshops where occasional cutting or grinding tasks arise. Unlike their professional counterparts, home grinders aren't designed for continuous, prolonged operation. Most manuals recommend giving the device a 15-minute rest after every 10 to 15 minutes of use.
Heavy loads, long non-stop use, a significant amount of dust and other factors characteristic of professional use of tools, require from manufacturers producing more expensive (professional) grinders, special technical solutions, precise manufacture of all parts and careful quality control.
Overall quality
Obviously, the more quality parts are used in the design of the tool, the higher the technological level of the manufacturer, where the products are assembled, the stricter the quality control — the price of the grinder will be higher.
The overall quality of a tool's parts and components is often evident at a glance. In the case of an angle grinder, signs of a lower-quality product (like a budget model or a counterfeit) may include noticeable play in the output shaft. Such tools are unsuitable for professional use as the play can cause irregularities and vibrations, hindering precise work. Cheap angle grinders may also exhibit lower-quality casting, with burrs on the body and gearbox, and imprecise casting boundaries. Manufacturers may cut corners on materials like plastic for the casing, rubber pads, cable length, and other details.
As always, the most interesting thing is inside the power tool. Exactly there are hidden those parts and assemblies that distinguish expensive grinders from cheap ones.
![]() |
The design of a small grinder. |
Electric motor
The electric motor serves as the core component of a grinder, but it's also one of the most susceptible to failure. Overheating and interturn short circuits in the windings are common culprits behind power tool breakdowns. High-quality motors found in pricier, professional angle grinders are easily identifiable by their epoxy-coated armature windings. This protective layer shields the motor from abrasive dust, a common byproduct of grinding and cutting tasks, preventing overheating, winding damage, and short circuits. However, budget grinders and counterfeit products often lack this safeguard. Instead, unscrupulous manufacturers cut costs by opting for cheaper varnish or even leaving the windings unprotected from dust.
Leading manufacturers prioritize the quality of materials used in electric motor construction, with a keen focus on specific attributes. For instance, they employ special steel for rotor plates, chosen for its ability to maximize magnetic flux while minimizing metal heating. Similarly, winding windings use specialized wire consisting of 97% copper, complemented by unique additives enhancing flexibility, strength, and wear resistance.
Quality control is a crucial step in manufacturing. For instance, Makita rigorously tests each electric motor, including a 3-minute operation at maximum load. In contrast, budget manufacturers often have lower standards for motor quality. As a result, the reliability and lifespan of motors in expensive and inexpensive angle grinders vary significantly.
Bearings and seals
No less important parts (from the point of view of the quality and reliability of power tools) are bearings. There are several of them in the angle grinder design (on the output shaft and the rotor shaft). More expensive angle grinders are equipped with good bearings from well-known manufacturers (NSK, SKF, CHL, etc.). Manufacturers of budget tools most often, in order to save money, buy bearings without markings, the origin of which cannot be determined.
The problem with cheap bearings is that the oil seals are of inferior quality. Dust and dirt can get in through the gap between the cage and the seal, causing the bearing to rotate worse. Good grinders are always necessarily present labyrinth seals that protect the bearings mounted on the rotor shaft from dust and chips. And budget MCDs and fakes are far from always boasting the presence of such dust protection.
Gearbox
Since the gearbox bears the main load during operation of an angle grinder, the quality of manufacture of all its parts is of fundamental importance for the reliability and durability of the tool.
A high-quality grinder requires a gearbox housing made from durable, lightweight materials with excellent heat conductivity, such as aluminium or magnesium alloys. The housing needs to be rigid to support the large gear, well shielded from dust to prevent rapid gear wear, and compact enough to fit into tight spaces like corners of metal structures.
![]() |
Internals of the angle grinder gearbox. |
Manufacturers of reputable grinders adhere to strict standards when producing drive and driven gears. These gears are crafted from special steel and undergo surface hardening to resist mechanical wear and handle heavy loads. Precise manufacturing is crucial for gear balancing and accurate tooth meshing adjustment. Budget angle grinder manufacturers lacking modern high-precision equipment may struggle to meet quality requirements. Consequently, cheap angle grinders often exhibit small backlashes and gaps, causing gears to generate more noise, heat up faster, and wear out prematurely.
Warranty and service
Famous manufacturers who care about their own reputation include a solid guarantee in the price of the grinder. They also maintain large networks of branded service centers and spare parts warehouses. For example, for angle grinders such as Makita or Bosch, almost anywhere in the world you can buy any part without any problems: even a gear, an armature with bearings, or a start button — everything that may be needed to repair an angle grinder. And local brands and Chinese brands, unlike global manufacturers of power tools, often save money, they do not spend money on warranty and service and do not worry about the supply of components necessary for repair of grinders.
Modern tendencies
New technologies are gradually making their way into the power tool industry. The most recent angle grinders are increasingly equipped with brushless motors, which have a lot of advantages (we talked about them in the article “Brushless screwdrivers: why they are better than conventional ones” using the example of another type of tool). It should also be noted that the demand for cordless angle grinders is growing, which are becoming more and more popular (both in the professional and home segments) due to the possibility of autonomous operation without connection to the power grid.
Compact brushless electric motors and high-quality battery units are very expensive products with complex electronic components. Therefore, modern brushless and cordless angle grinders are much more expensive than tools with a traditional design and mains power.
![]() |
Cordless grinder with brushless motor. |
Electronic features
The price of an angle grinder is also greatly influenced by the presence or absence of various electronic gadgets that provide additional functions and capabilities.
The most useful and popular functions are:
- speed control — allows you to adjust the desired spindle speed, selecting the optimal rotation speed for working with different attachments and materials;
- maintaining momentum — the angle grinder automatically maintains the set rotation speed, despite changes in the load on the spindle;
- soft start — the starting current limiter, built into the electrical circuit between the button and the motor, protects against current overload during motor startup and ensures a smooth acceleration of the attachment without any jerking;
- overload protection — in case of overheating or overcurrent, the motor automatically turns off to avoid irreversible damage to the windings on the armature and stator.
Each of these functions is provided by a separate module or electronic board, which increases the cost of the angle grinder. Therefore, such feature are much more common on expensive grinders than on cheap ones.
Safety and comfort
Design solutions that ensure safety, comfort for the user and increased productivity also affect the cost of the angle grinder. On more expensive (professional) grinders the following are more common:
- motor brake — a device that stops a disc rotating by inertia in 2 — 3 seconds;
- safety clutch — a mechanism that breaks the mechanical connection between the spindle and the gearbox to protect the angle grinder from damage when the disc jams;
- keyless disc chande — allows you to install and remove attachments without a special key and thereby saves a lot of time;
- keyless housing adjustment mechanism — eliminates the need to use a screwdriver to rotate the protection to the desired position;
- dust collector — allows you to connect a vacuum cleaner to the angle grinder to remove dust from the working area.
Brief conclusions
As shown above, the cost of an angle grinder is influenced by many factors. The final price of an angle grinder consists of a huge number of little things that the average buyer does not think about or does not know at all.
When choosing a tool for professional use, emphasis should be placed on reliability (the ability to withstand long-term heavy loads) and maintainability (availability of spare parts and availability of service). And for occasional home use may well be suitable not so advanced models, but much cheaper grinders from budget brands, producing devices of DIY class.
Information about many characteristics and nuances of angle grinders can be found in our catalog. And some features (such as the actual service life or repair features of a certain model) can be learned exclusively from reviews written by tool owners based on personal experience.
Articles, reviews, useful tips
All materials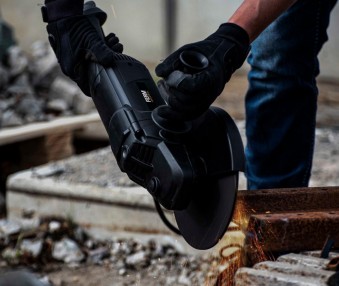


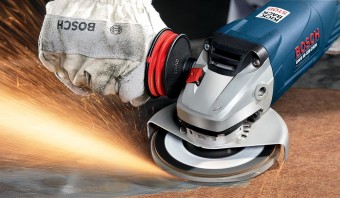
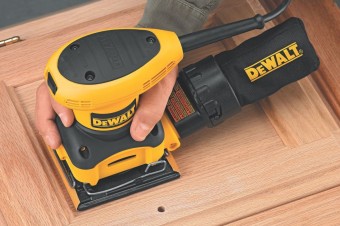
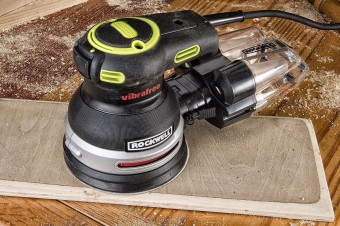