Which car wheels are better: stamped, cast or forged?

As Henry Ford once said, the appearance of a car is 70% dependent on the installed disks. Also, the wheels play an important role in the controllability of the machine, the dynamics of movement, affect fuel consumption. The simplest option for car rims are steel or forged wheels, which are good for daily use as they are cheap and durable. In addition, steel wheels are easy to repair and replace. Many "factory" disks for inexpensive cars belong precisely to the category of "stamping".
stamped discs
Steel wheels are the simplest and cheapest type of car rims. They are also often referred to as stamped. The components of such discs are made of sheet steel on special presses by cold stamping. The workpiece is stamped on them, and the rim is rolled into a figured strip, bent into a ring and its ends are welded. The unpretentious technology for the production of steel discs entails the cheapness of "stamping". The plasticity of the material allows steel wheels not to burst, but only deform upon impact. Moreover, the wheel geometry is preserved to a certain extent and there is a possibility that the tyre will not depressurize.
![]() |
As a rule, stamped discs look simple and unpretentious. |
The downside of stamped discs is their heavy weight. Moreover, it is not possible to reduce it, since a decrease in the thickness of the steel sheet would entail a deterioration in the strength characteristics of the wheel. Also, steel does not resist corrosion well. Another disadvantage of this type of disc is the poor design. With rare exceptions, stamped wheels look plain and archaic. Often they completely spoil the appearance of the car. However, steel wheels can always be embellished with car caps.
In contrast to the "stamping" wheels are made of light alloy metals. Such discs can be given a variety of shapes, and in appearance they satisfy the tastes of the most demanding audience of car owners. A rich assortment in terms of design is by no means the only advantage of alloy wheels. Before revealing their other advantages, it is necessary to dwell in more detail on the technologies for the production of "light alloys".
According to the method of manufacture, there are two main categories of alloy wheels: cast and forged. The vast majority of them are made from alloys of aluminium, copper and magnesium with the addition of a small amount of other metals, the proportion of which often does not exceed 5%. The preparation of alloys for the manufacture of cast and forged wheels is plus or minus the same: the necessary metals are melted in huge vats and all this is cooked until a homogeneous mass is reached. But further casting and forging technologies are strikingly different.
Alloy wheels
In the manufacture of this type of discs, low pressure casting technology is used. Actually, this is where the name of alloy wheels came from. Hot metal alloys are poured into special molds, the metal in them cools naturally and the product takes on its final appearance.
![]() |
A variety of shapes and designs for relatively modest money is a key advantage of alloy wheels. |
Finished wheel castings undergo heat treatment to harden the wheel and relieve internal stresses in the metal. Then it remains only to mechanically process, grind and polish. The key benefit of casting is that discs can be molded into almost any shape, allowing for a variety of design options. However, the technology is not without its downsides.
In the casting process, voids and shells are often formed, and the metal itself has a characteristic porous structure. These factors weaken alloy wheels somewhat and increase the tendency to form microcracks. From strong blows, they often split or crack. Repair of alloy wheels is carried out on specialized equipment and is not cheap, and in a good way, a badly damaged disk is sent for recycling.
![]() |
Repair of alloy wheels is expensive and is performed on specialized equipment. |
The problem with strengthening the strength characteristics is partly solved by thickening the disk and rim. As a result, cast wheels are heavier than forged ones, but lighter than stamped ones. The lighter weight compared to steel rims improves vehicle handling and reduces fuel consumption. At the same time , alloy wheels are better balanced, and in terms of a variety of beautiful and stylish designs, they cannot be found at all.
Forged wheels
Forged wheels are produced by volumetric hot stamping followed by machining. The process of their production is very complicated and is carried out in several stages. In the first step, the molten metal alloy is poured into round narrow molds, from which long round ingots are obtained in the form of cylindrical pillars. They are sawn into smaller pieces and sent to a press, where the blanks are squeezed under tremendous pressure to prevent the formation of air microvoids in the finished product.
Using different forms of the press, the blanks gradually take the form of a disk. But without characteristic beams and holes, the design of the blanks remains monolithic. The future disk is heated in a furnace to high temperatures (about 500-600 ° C) and cooled sharply, thereby “forging” the metal, hence the name. At the next stage, the disk undergoes an artificial aging procedure, which makes it possible to remove the stresses arising in the process of deformation. Aging is carried out in a special oven for a long period of time (from 12 hours).
![]() |
The blanks of forged wheels take their final form on turning and milling machines. |
Forged wheels acquire their final form on turning and milling machines, where they form the design of the future product with special drills and cutters. At the final stage, the finished disc is ground and polished to a mirror finish, engraved and company logos are applied, and coated with a protective compound.
In terms of strength characteristics, forged wheels are clearly stronger than steel products. This ensures the highest rigidity of the structure and corrosion resistance. And thanks to excellent plasticity, forged wheels do not collapse after strong impacts, but are deformed in the manner of “stamping”, which guarantees good maintainability.
By weight, forged wheels are about 20-30% lighter than cast ones and 30-50% lighter than stamped ones. Reducing the mass of the wheel favorably affects the improvement of the suspension of the car. As a result, the level of driving comfort is increased, good dynamics and controllability of the machine is achieved. However, forged wheels are more expensive than other counterparts.
![]() |
Forged wheels are the most expensive, so they are most often installed on the wheels of premium cars or sports cars. |
Also, the so-called forged hybrid products are often included in the category of such disks. However, they are cast and manufactured using other Flow Forming or Hybrid Forged processes. These are lightweight cast wheels, which only approach the strength properties of forged ones. However, they are clearly cheaper in terms of production technology, which is why they are also interesting to buy.
In the categories of cast and forged wheels, products with a hidden bolt pattern are often presented. The fixing bolts in them are covered with a decorative cover to match the overall design of the disc. The hidden bolt pattern improves the appearance of the wheel and prevents clogging of the mounting bolt heads.
How to tell forged wheels from cast wheels?
In the same size, forged wheels differ from cast wheels in a lighter design. For example, a conditional forged disk with a landing diameter R15 should weigh about 4-5 kg, while the “casting” in this size has a weight of 7-8 kg. An exception to this rule are forged wheels produced using outdated technologies - they are almost the same in weight as cast ones.
The visual differences between forged and cast wheels lie in the shape of the edge of the disc and the nature of the application of technological inscriptions. The edge of forged wheels is always even, and the markings on them are depressed. In alloy wheels, the edge may have irregularities, and the inscriptions are made convex. Forged products are also marked with the “forged” stamp.
For better clarity, a comparative description of common types of car rims is given in a summary table:
Material | Manufacturing technology | Weight | Strength | maintainability | Design | Price | |
---|---|---|---|---|---|---|---|
![]() |
Alloys of aluminium, copper, magnesium | Volumetric hot stamping with machining | Easy | high | Good | For every taste | High |
![]() |
Metal alloy (Aluminium based) | Injection molding | Average | Medium (with strong impacts, the disk is destroyed) | Low (requires special equipment) | For every taste | Medium |
![]() |
Steel | hot pressing | Big | Satisfactory (good elasticity) | Good | Basic appearance | Low |
prefabricated models
The advantages of forged and cast wheels are successfully combined in a separate caste of prefabricated models. Typically, they consist of a forged rim and a cast "saucer" held together with high-strength titanium bolts. Such disks can be made both in a monolithic form and collapsible, which implies the possibility of dividing the wheel into structural components. The user has the right to replace the "plate" with another, thereby changing the "pattern" of the disc. And if the rim is damaged, you can only change it.
![]() |
Prefabricated disks are assembled from several components, fastened with titanium bolts. |
Prefabricated disks are the most rare. Many of them are made to order and in most cases serve as a fashion element in the design of the appearance of the car. It should be noted that not only the rim from the “plate”, but also the central flange, spokes, individual parts of the rim, a retaining ring, etc. can be separated in the design of prefabricated disks.
Prefabricated wheels are not a cheap pleasure. Their high cost is due to high-strength characteristics, design variability and implemented design tricks such as beadlocks (Beadlock), which fix the tyre rim, and taerlocks (Tirelock), which prevent wheel disassembly in case of punctures or loss of pressure.
The category of prefabricated models most often includes discs with a characteristic shelf, visually increasing the width of the wheel. The shelf on a disk is a raised edge wide enough to allow an object to be placed on it. They put such discs on the wheels of powerful sports cars or high-torque classics to give the car a sophisticated look.
Summarizing what has been said, stamped wheels are the most affordable and simple, cast models will please with a variety of designs, and forged products belong to the top segment. The most chic is the assembled wheels, however, they are the most expensive.
The key nuances of choosing discs by diameter, size of the central hole, width and offset are described in detail in the article “How to choose wheels for a car so that they will surely become?”.
Articles, reviews, useful tips
All materials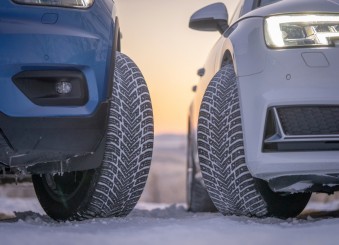

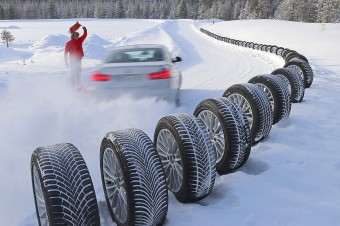
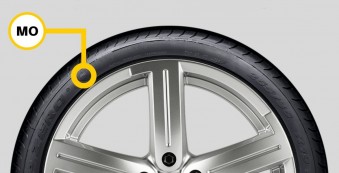
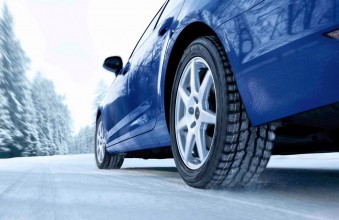
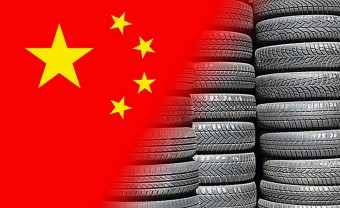