Drill chuck: types and differences

Features of drill chucks
The function of the drill chuck is to hold the tool on the spindle. In fact, the chuck serves as an adapter between a tool and a working attachment.
Jaw chucks are the most widely used in the power tool industry. In the center of the chuck there are three interdependent jaws that synchronously move together to clamp the tool shank or move out to release it during rotation.
Advantages of three-jaw chucks:
- versatility — tools with round shanks (drills) or hexagonal shanks (bits) can be clamped;
- changing the size —the jaw mechanism provides the possibility to use the same chuck for fixing the equipment of different sizes (drills and screwdrivers are usually equipped with chucks with a diameter of 1 — 10 mm or 1.5 — 13 mm).
Of course, they also have some disadvantages. The main one is the risk of clogging of the mechanism (dust, metal chips or construction waste), which leads to jamming of the jaws. It is also worth mentioning that there is a risk of the round shank rotating in the jaw chuck if the torque is too high (therefore, other types of chucks have been developed for some tools, which will be discussed below).
Design and principle of operation of a jaw drill chuck:
Keyed and keyless chucks
Depending on the method of rotation of the adjusting sleeve, by means of which the jaws are tightened, chucks of this type are divided into keyed and keyless.
Keyed chucks have a gear teeth around the perimeter. The rotation of the gear drives the jaws that clamp the tool. The keyed chuck is tightened with a special chuck wrench with splines meshing with the teeth of the gear.
The advantages of keyed chucks are the ability to tighten the jaw mechanism with the high torque required to secure the tool and the high reliability of the solid metal construction. The disadvantages include the need to use an auxiliary tool (wrench), not a very fast tool change process and the need to use both hands.
![]() |
A classic keyed chuck which design was patented back in 1902. |
Keyless chucks, unlike keyed chucks, are tightened and unscrewed solely by hand strength. Therefore, replacing equipment takes significantly less time. Keyless chucks come in single- and double-sleeve versions.
- The double-sleeve keyless chuck consists of two halves. To loosen or tighten it, the rear sleeve must be firmly pressed with one hand and the front part rotated with the other. This design is characterized by reliability, simplicity and a much faster tool change process than keyed chucks.
- The single-sleeve keyless chuck has only one external sleeve. By rotating it with one hand, the jaws can be moved to fix or release the working attachment, while the other hand remains free for other actions. Single-sleeve chucks are the most user-friendly, but they can only be used on tools that have an output shaft lock.
![]() |
The single-sleeve chuck (on the left) is turned with one hand, and the double-sleeve chuck (on the right) with two. |
Keyless chucks are more often found on drills and screwdrivers of the middle power class. They are convenient and practical (especially if you need to change attachments frequently). But it should be noted that chucks of this type do not very reliably fix large-diameter drill bits, and the jaw mechanism inevitably wears out due to constant screwing and unscrewing (with more or less intensive use of the drill, you have to change the chuck every couple of years). Keyed chucks, which provide a high degree of reliability in fixing drill bits, are much better suited for powerful drills.
Bit holder
The bit holder is found on many screwdrivers and some drills (especially on those models that have a controller that can adjust the speed of the attachment). This chuck is a hexagonal hole in the output shaft that is sized and shaped exactly like a standard bits. Magnets or locking mechanisms with spring-loaded balls can be used to fix the attachment inside the hole — both are quite reliable and easy to use. This chuck allows the tool to screw and unscrew fasteners or use accessories with hexagonal shanks (drills and bits of this type are available on the market).
SDS+ and SDS-Max chucks
As mentioned above, jaw chucks are not well suited for high torque tools and large drill bits (more than 16mm). Therefore, other types of chucks and special equipment were developed for rotary hammers. In SDS+ and SDS-Max chucks, instead of movable jaws, specially shaped slots and specific locking mechanisms are used to secure the shanks. The splines transmit torque from the shaft to the attachment and center the tool in the chuck. And the clamps (balls or rollers, depending on the design of a particular mechanism), falling into closed grooves, prevent the shank from falling out of the chuck.
SDS+ chucks are more often used on mid-power hammer drills designed for drilling and demolishing less dense materials (for example, brickwork, wall blocks, etc.). SDS-Max is a reinforced version for working with larger attachments, which differs from SDS+ in size, shape of internal channels and the way the shanks are mechanically fixed. SDS-Max chucks are more commonly found on large, heavy, high-impact hammer drills designed for demolition work.
![]() |
Drill bits of the same diameter with SDS-Max (above) and SDS+ (below) shanks. |
SDS+ and SDS-Max accessories (drill bits, blades, chisels, saws) are not suitable for use with drills equipped with jaw chucks (and vice versa). Compatibility can only be achieved using special adapters.
Metal or plastic
All internal parts of the drill chuck, regardless of its design, are made of metal. Particular attention is paid to the strength of the jaw mechanism and the hardness of the working surfaces of its jaws. The rotating chuck sleeves can be entirely metal (more often found on drills) or made of impact-resistant plastic (this design is used on many drill drivers). All-metal chucks are more durable and reliable, while plastic chucks are lighter and cheaper. There are often chucks that have a combined design: the metal base is covered with plastic to make it more convenient for the user to fix the tool manually.
![]() |
Screwdrivers with metal (left) and plastic (right) chucks. |
Drill chuck arbor
Connecting the chuck to the output shaft of a drill or screwdriver can be accomplished in several different ways. The most common arbor types include:
- threaded — the chuck is screwed onto the output shaft. Depending on the manufacturer, metric or inch threads can be used.
- conical — the chuck is held in the seat by the friction force between the surfaces of the outer cone and the inner cone;
- quick change — a function that allows the chuck to be fixed and released by turning the lock, pulling the ring or otherwise. This type of chuck fixation is mainly found on screwdrivers and drills with low power.
The design and size of the arbor are important, first of all, when choosing a new chuck for a drill instead of a worn-out unit.
Brief conclusions
There is no perfect chuck that will satisfy the needs of all users without exception. For example, an all-metal keyed chuck is reliable and holds the tool firmly, but it is heavy and requires you to always keep a wrench with you. And keyless analogs allow you to change attachments faster, if you need to switch from one type of work to another, but at the same time it can lose the drill bit under heavy loads. Therefore, when buying a drill or screwdriver, you should choose a tool with the type of chuck that best suits your way and speed of drilling.
Articles, reviews, useful tips
All materials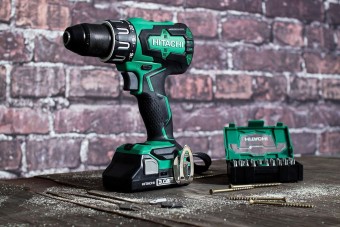

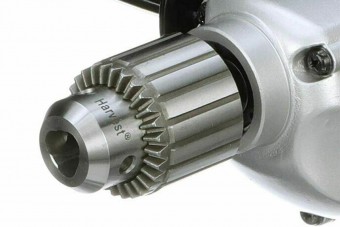
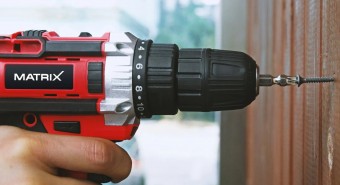
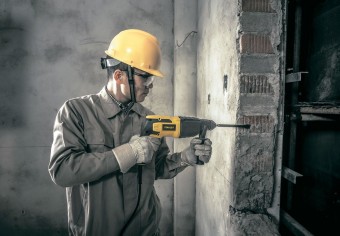
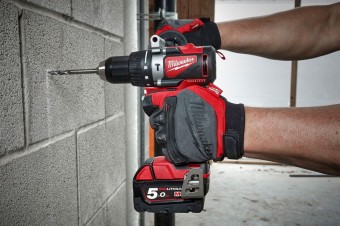